Features/Application
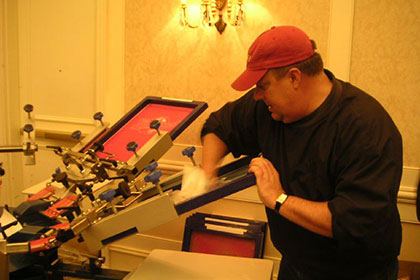
Best suited for fine line graphic images, transfer paper applications.
Excellent resistance to water and superior durability.
Consistent emulsion thickness profile over the mesh, Lower Rz value.
Good adhesion to screen mesh.
Wider exposure latitude.
Recommended for printing with water based inks and pastes.
Suitable for T-shirt, Textiles and wider range of printing applications.
Specifications
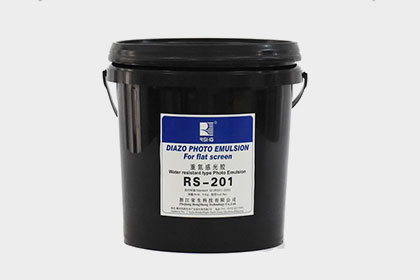
Viscosity: Approx. 3000-3500 mPa・s, 25℃
Solid Contents: Approx. 40-41%
Packaging Standards: 1kg set, 5kgs set.
Contact us for custom packaging.
Exposure Data
Screen mesh, Color | E.O.M (μm) | 2Kw Metal Halide lamp |
Polyester 31/cm (80/inch) w | 5 | 70-90 sec. |
Polyester 31/cm (80/inch) w | 15 | 280-350 sec. |
Polyester 59/cm (150/inch) w | 5 | 35-45 sec. |
Polyester 59/cm (150/inch) w | 15 | 280-350 sec. |
Polyester 100/cm (250/inch) w | 15 | 300-360 sec. |
※The above is for guideline purposes only, kindly to use a gray scale exposure calculator to identify optimal exposure time.
Solvent Resistance Rating
Solvent | Rating | Solvent | Rating |
Water | Excellent | Turpentine Oil | Fair |
Conventional Solvents | Poor | Citrus based chemicals | Fair |
※24 hours swelling/absorption test results.
Instructions
Wash, degrease and dry screen mesh. Remove grease and foreign contaminants with MSP cleanser.
Dissolve provided Diazo with 10% water to emulsion volume. Please do not use warm water.
Pour Diazo solution into emulsion. Mix it well. Prior to a use, let mixed emulsions settle for one day.
Or for immediate use, filter it with screen mesh 100/cm or higher.
Coat emulsion slowly in order to prevent air bubbles.
Dry coated screen completely at temperatures up to 40℃ (104℉) before exposure.
Remarks
Keep the mixed emulsion in a cool and UV light safe area. Use mixed emulsion within 2 weeks.
Recommended to filter remaining emulsion with screen mesh before pouring it back into the container to remove any dust, foreign substances and air bubbles.